About us.
We put people first.
What sets us apart from other employers is our special, grounded corporate culture that puts people first. Because we know that our success is based on the commitment of our employees.
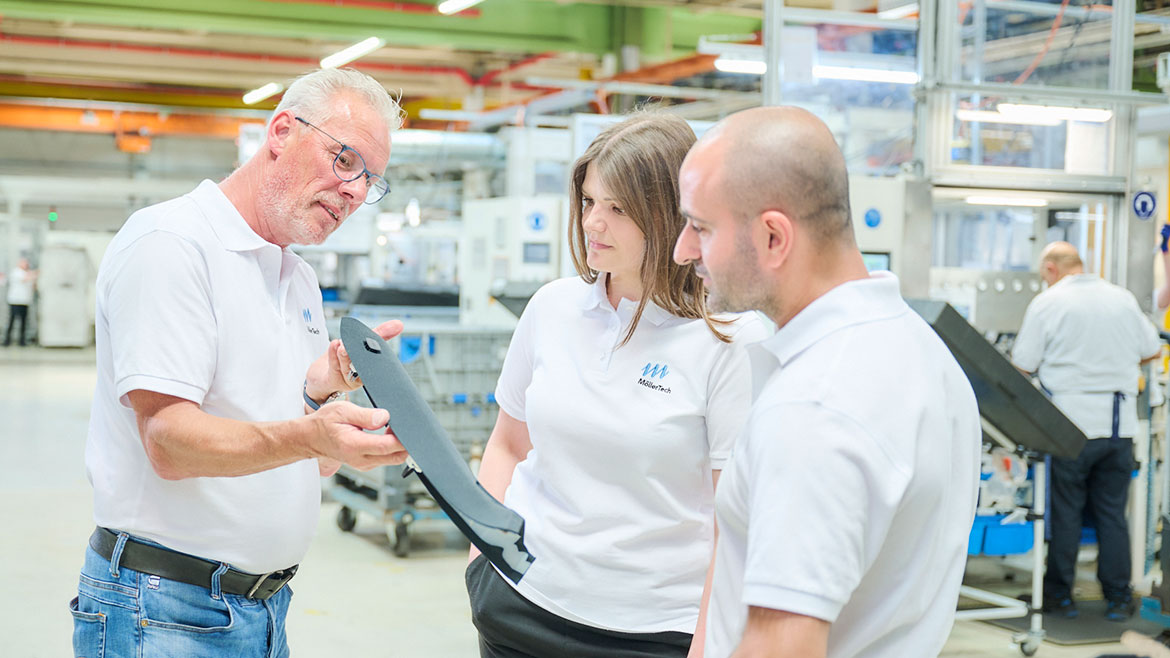
Shaping the future together.
Made by people since 1730.
Everything we do is characterized by transparency, team spirit, and cooperation. We offer our employees the freedom to actively contribute, to develop personally, and to shape the future together with us.
We are well aware of our achievements and our exceptional expertise, but we are not removed from everyday challenges in the industry. Even if everything doesn’t always go perfectly or click into place on the first try. We are authentic and also persuasive because of our inner values. That’s what our employees appreciate.
The heart of our corporate culture.
MöllerEconovation – the Kaizen philosophy taken a step further.
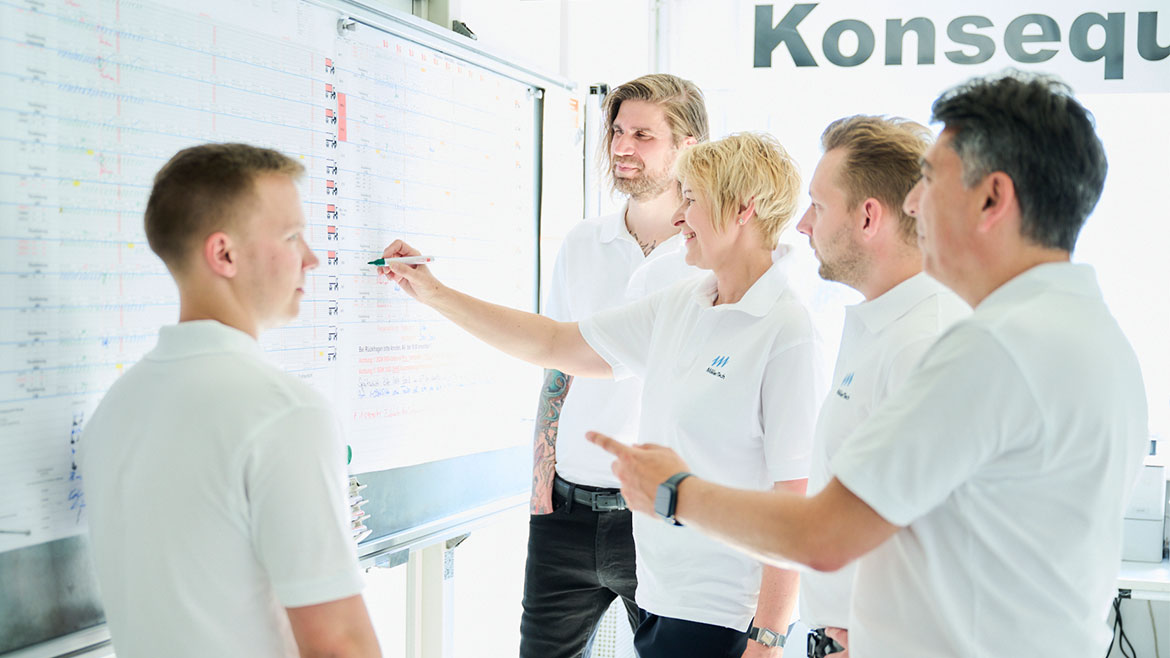
MöllerEconovation is an innovation that takes the proven Kaizen philosophy a step further. The term Kaizen is Japanese: “kai” means change and “zen” for the better—and this is at the heart of our corporate culture. MöllerEconovation combines “economy” and “innovation”. MöllerEconovation enables us to define internal activities and processes even more precisely across all process steps and to optimize them permanently.
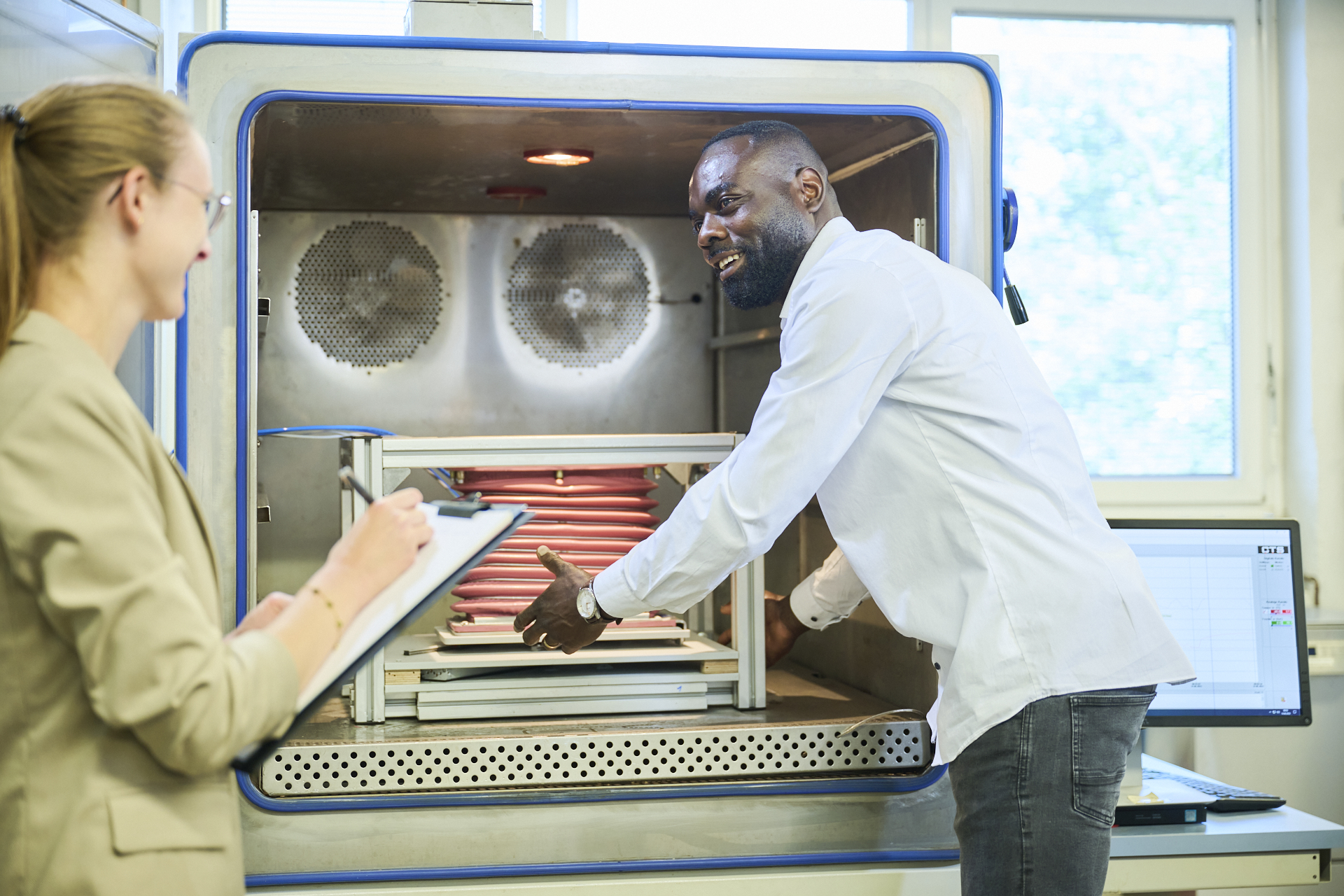
In doing so, we focus on our employees because they are the key to our success. We give them responsibilities but continue to offer support. As a partner and companion, we encourage personal initiative and at the same time support employees so that they can develop their skills to the best of their abilities.
Benefits.
Joining our team benefits you.
Our team’s special dedication and the bond within the Group are the basis of our success. These are things we truly appreciate. And that’s why our fundamental goal is to create a framework in which everyone can actively shape their everyday working life, even if unexpected challenges sometimes arise. Our core benefits and supplementary benefits are just a small part of what we do to make everyone feel at home.
Vacation and flexibility.
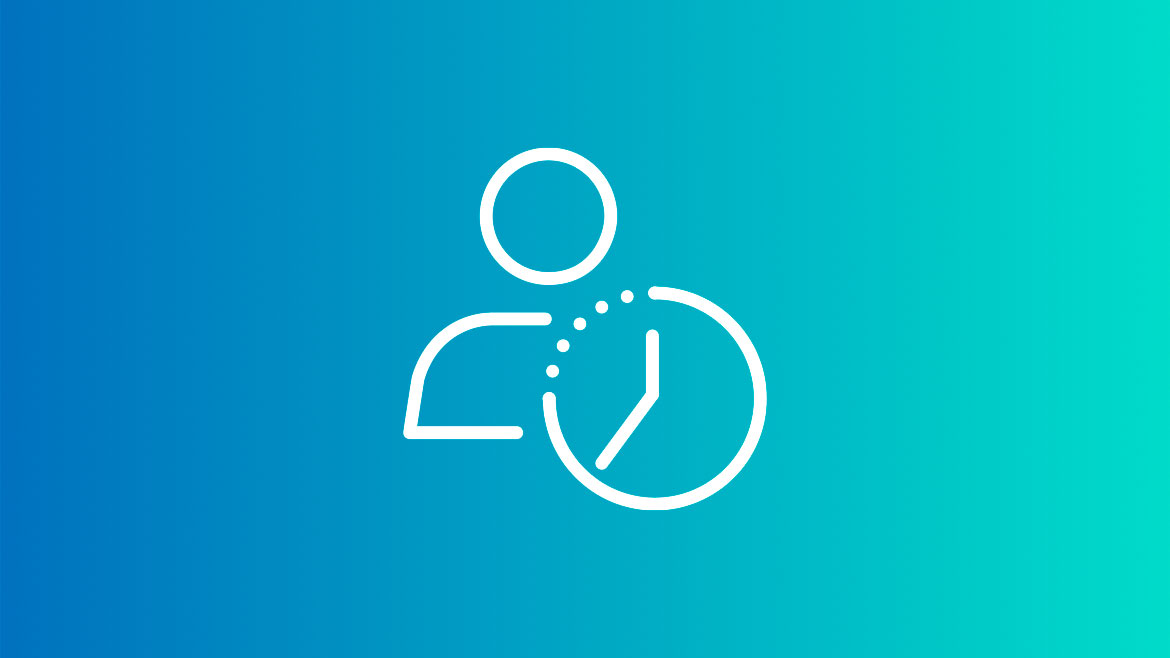
- Flexible working-time models
With flexible working-time models such as flex-time and the option to work mobile on a regular basis, salaried employees can organize working hours individually and find an optimal balance between professional and private life.
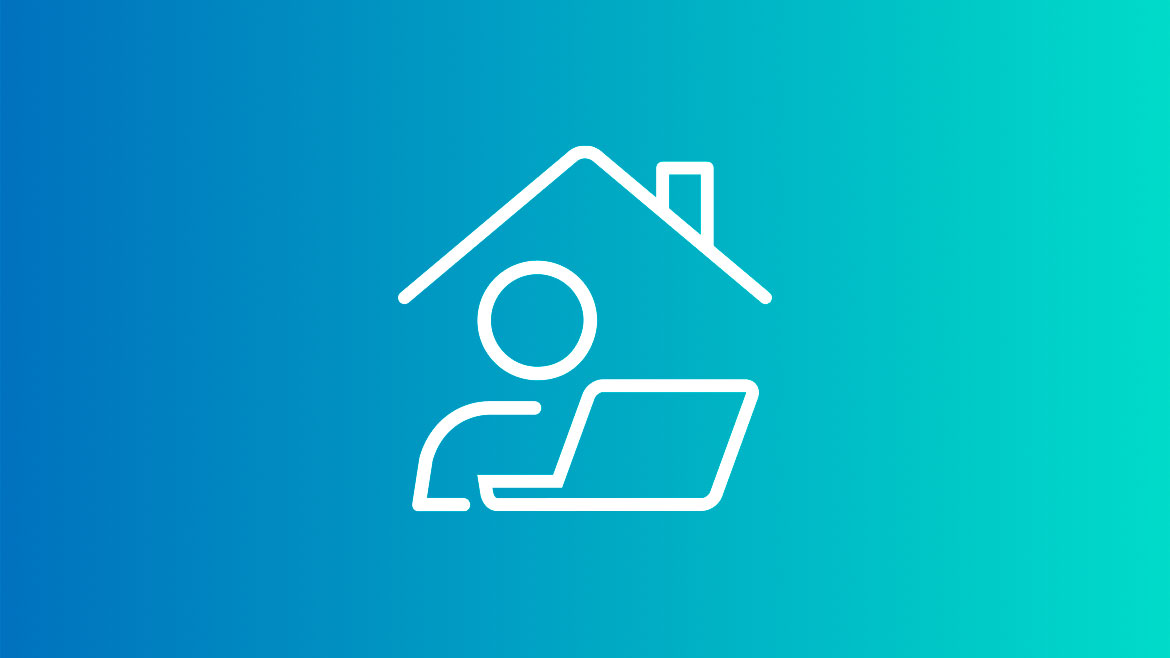
- Mobile working
Hybrid, remote, and on-site working are possible with us, as long as it is compatible with your function and tasks. The basic prerequisite for this is, of course, that you also have the appropriate environment at home.
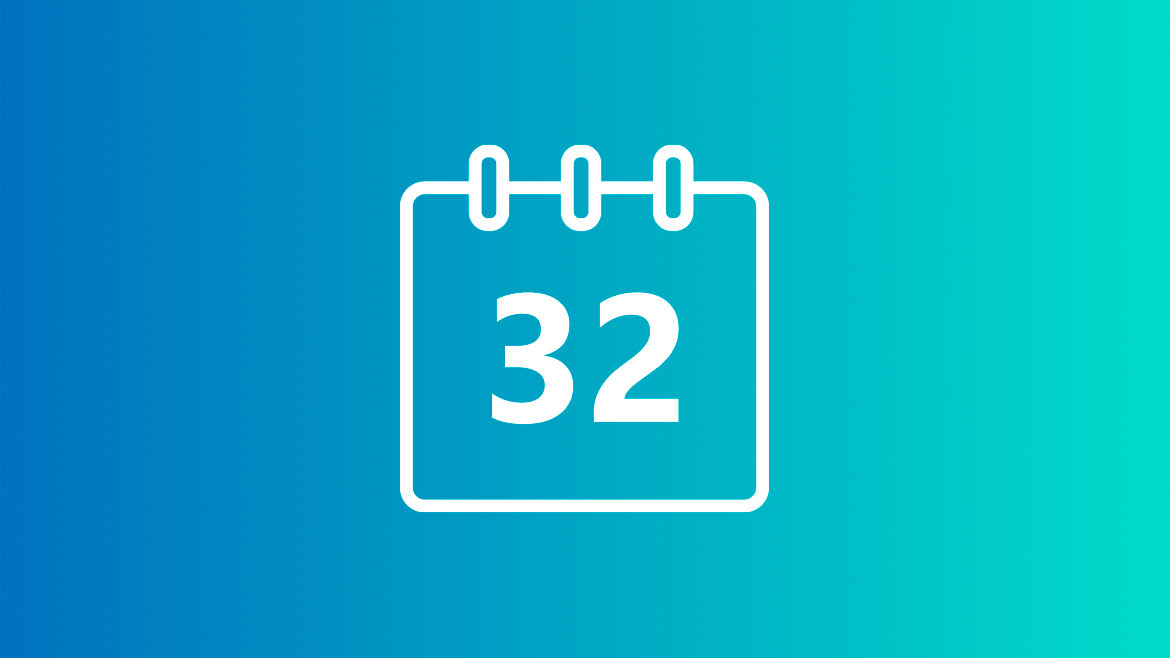
- Up to 32 days paid vacation
Here, you are entitled to at least 30 vacation days. In addition, you have the option of receiving two days of additional vacation in lieu of increased vacation pay, allowing you to extend your vacation entitlement to 32 days!
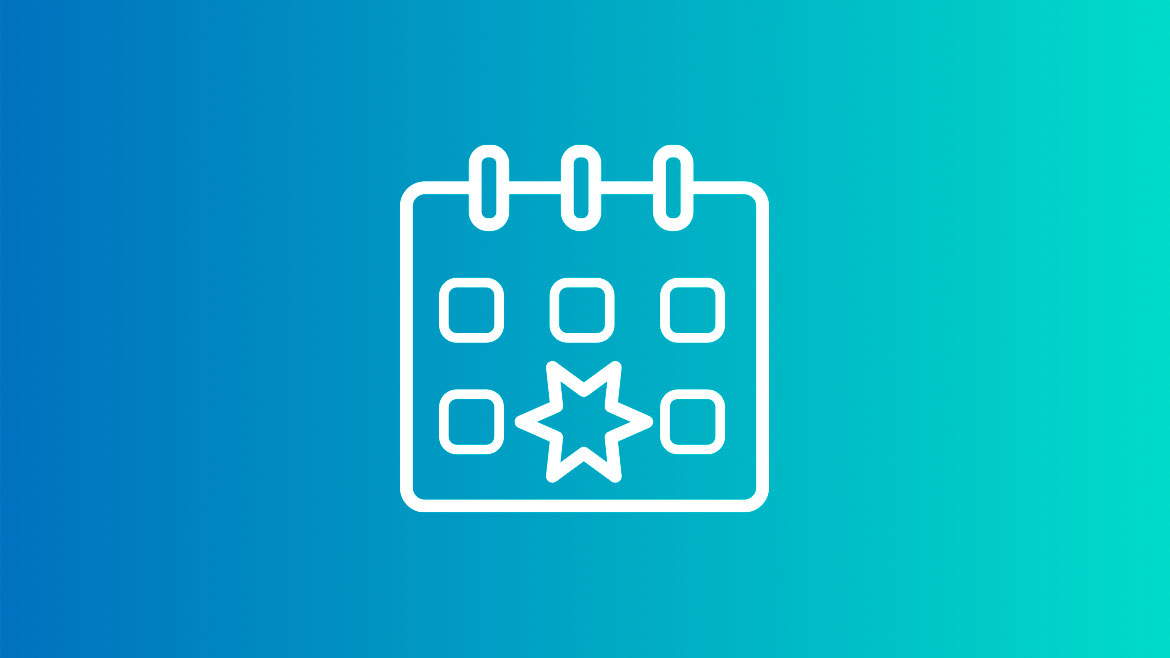
- Special paid leave
You will receive up to 4 days of additional special paid leave for a variety of occasions. This is granted, for example, for your own marriage, the marriage of a child, the birth of a child, a move, or a company anniversary.
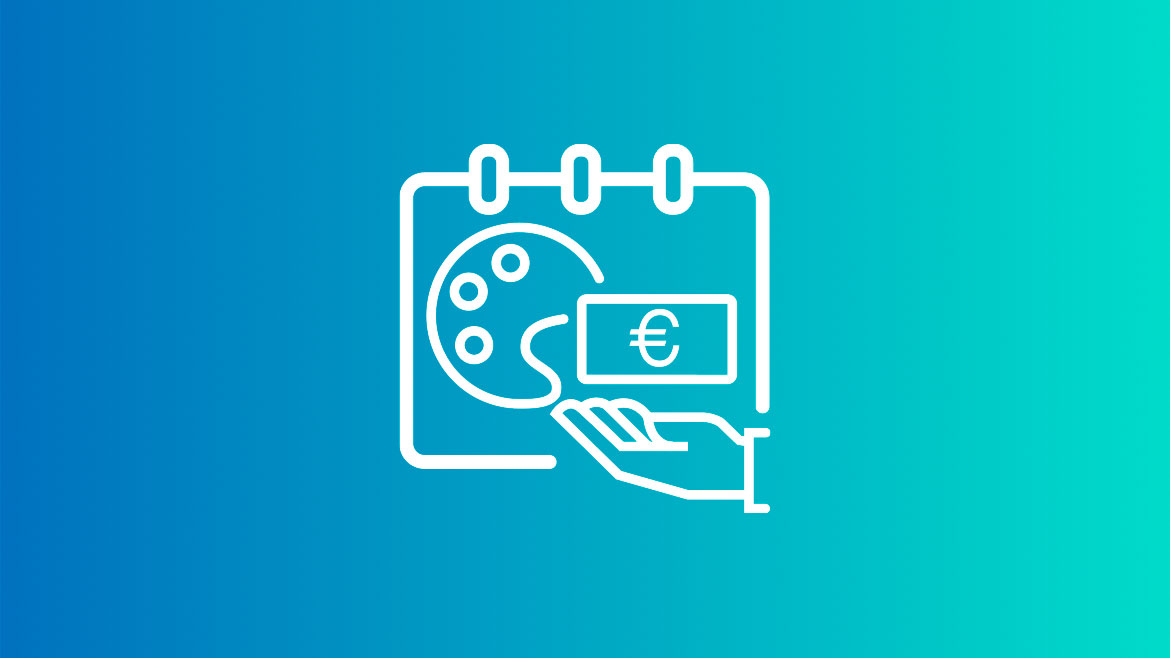
- Lifetime working time account
Life doesn’t always go as planned and your personal situation may change. For these situations we offer a lifetime working time account. The employer pays an annual amount into this account and you also have the option of paying into this account. The lifetime working time account is designed to finance longer periods of time off, e.g., before retirement, to care for relatives, or in the form of a sabbatical. With this lifetime working time account, dreams of a 4-day work week or time off can come true!
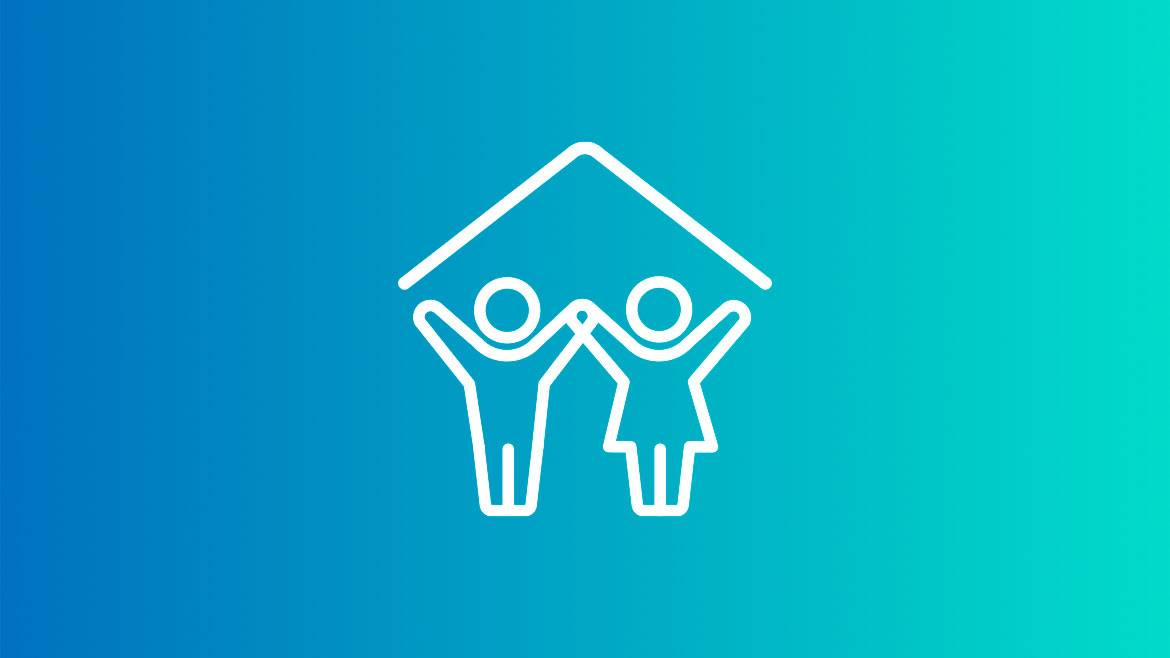
- Our daycare center
Our location in Bielefeld runs a company daycare center called “MöllerNest.” You can request a spot for your child depending on availability. In addition to care for very young children (starting at the age of 4 months), the company daycare center offers long hours of operation, which also ensures care for children of our employees working shifts.
Compensation elements.
- Vacation and Christmas bonuses
We want our employees to be able to enjoy special moments, so they receive a total of more than a 13th month’s pay each year in the form of Christmas and vacation pay.
- Jobticket
Protecting the environment and saving money at the same time.
Whether you’re on your way to work or you regularly use public transport in your free time, with the Jobticket or the Deutschlandticket you can travel inexpensively on local or long-distance trains. The best thing is that we take care of the tedious contract processing and billing for you. - Retirement benefits and tax-free compensation
to employees for capital accumulation purposes help you look to the future with confidence.
The company pension plan is an important building block to help reduce the gap between your income at work and your pension in retirement. In addition, tax-free compensation to employees for capital accumulation purposes help you build up your private assets. - Employees recruiting employees
Do you know someone who would be a perfect fit for the Möller team?
Through our referral program, you have the opportunity to refer your acquaintance to an exciting job and, at the same time, receive an attractive bonus for your referral. - Performance bonus, collectively agreed compensation and profit-sharing
More than just your salary.
Your standard pay is supplemented by a performance bonus of up to 9%. In addition, each employee receives a share of the company’s profits, which depends on the success of the company as a whole. - Partnership with DSC Arminia Bielefeld
As one of the oldest production companies in Bielefeld, we support DSC Arminia Bielefeld with passion. Our employees also benefit from this. We offer various special promotions in connection with our home soccer team
- Employee offers through Corporate Benefits
Our employees benefit from discounts at online stores and from regional suppliers. Attractive offers from many different brands can be found in the Corporate Benefits portal.
Health.
- Corporate health management
Your health is important to us which is why we offer systematic and integrated health management. Some examples are ergonomic consultation and adjustments to workstations, manufactured customized hearing protection, anti-fatigue mats in production areas, or health courses for well-being. We also support you in applying for assistive devices.
- AWO (Workers’ Welfare Federal Association) health services
Anonymous, confidential, and free of charge. Together with the AWO, we offer our employees psychosocial counseling as part of our Employee Assistance Program (EAP). The AWO and its experts offer advice on various topics such as caring for relatives, mental and physical stress, problems in partnerships and family, conflicts at work, and much more.
- JobRad bicycle leasing
To work, in everyday life, on vacation, or for physical activity—together with JobRad we offer you the option to lease bicycles. We handle the billing and you save up to 40% compared to a conventional purchase.
- Fitness studio membership discounts with SportNavi
We want you to stay fit. That is why we have partnered with the fitness studio SportNavi to offer our employees exclusive membership discounts. In addition, we regularly offer courses and active breaks directly on the company premises so that you can try out different sports (e.g., boxing) in a relaxed environment.
- Prevention and other offers
In cooperation with external partners such as health insurance companies, doctors, and other service providers, we regularly support various initiatives and services for preventative health and health management. In addition to vaccination opportunities, these include health management and preventive care programs as well as individual care from our company physician.
- Events and activities
In addition to regular health days on various topics, we offer our employees the opportunity to participate in various sporting events, such as the Easter Run, company runs, or run & roll Day. We also support our employees in participating in social events.
- Healthcare for trainees
Healthcare is not just for older people. Young people in particular are exposed to certain stressors when they start their careers. Recognizing these stressors is the first step in the right direction. For this reason, we offer seminars focusing on health specifically for our trainees and trainers.
Professional development and career paths.
- Professional development and promoting career paths
It goes without saying that we support our employees in all phases of their professional lives and enable them to develop their personal careers. In addition to offering a training catalog of e-learning courses and seminars, we also facilitate cross-mentoring programs.
- Working abroad/international assignments
With a large number of international locations, we make it possible for our employees to work abroad, even for a longer period of time. We support you in both preparing for your assignment and in returning to Germany.
- News
To ensure that you are always informed about the latest company events, our employees receive a Möller newsletter every six months featuring cross-company topics. You can also keep up to date with news on the intranet.
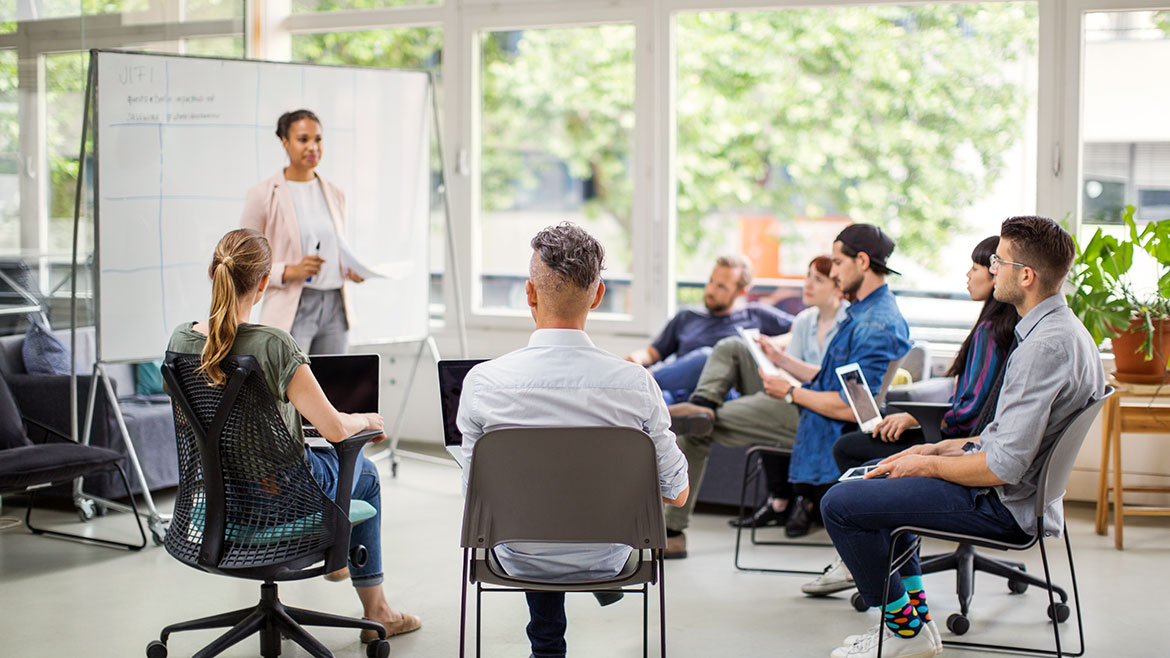